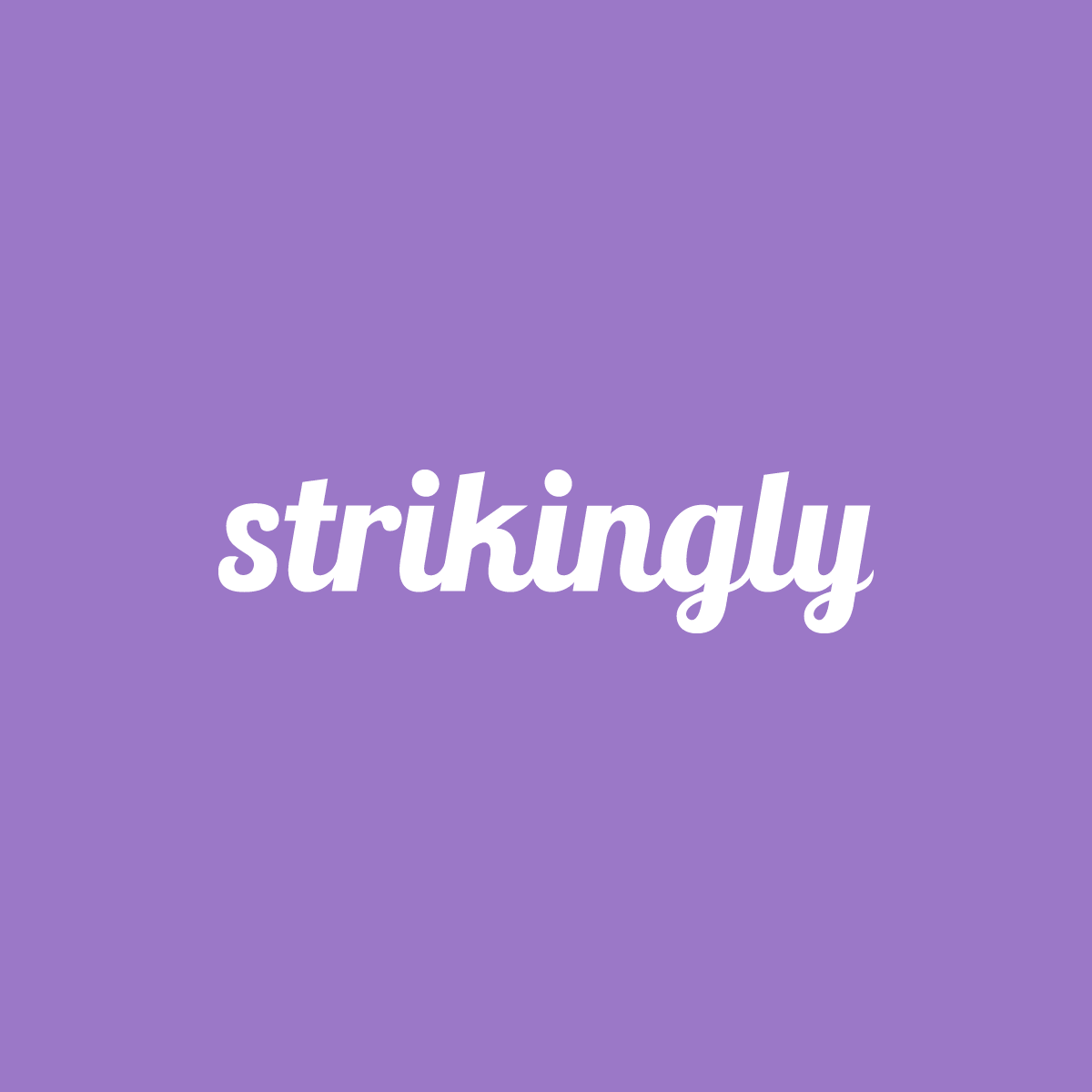
Quality Prism Masonry Color Integral
With Prism Pigments Masonry Color infinite possibilities exist. Our masonry colors when added to your concrete masonry unit or mortar mixture can be formulated to complement or contrast any masonry material being used on a project. Whether you are mixing mortar color on site or mixing large batches of colored block at the plant, our premeasured packages of color assure color uniformity from batch to batch. Prism Pigments masonry colors are blended from pure synthetic iron oxide pigments and they are lightfast and weather resistant.
Masonry color data
Description
Prism Pigments Concrete Colors are pure, synthetic iron oxide pigments containing no fillers that will affect the performance of the concrete mix design. Prism Pigments concrete color applications provide the user with a lightfast, weather resistant, lime-proof, no maintenance finished product. Prism Pigments maintain the highest tinting strength and color consistency from bag to bag. Prism Pigments Concrete Colors are ideal for use for integrally colored concrete in highly visible areas such as driveways, patios, walkways, car paths, curbings, athletic courts, or stamped concrete. A stable, weather resistant color is always the end result.
Composition and Materials
Prism Pigments Concrete Colors contain only finely milled synthetic iron oxides, the strongest and most stable colors available. These colors are lime-proof, sunfast, inert, and meet or exceed the criteria of ASTM C979.
Colors
Prism Pigments Concrete Colors cover the full color spectrum: brown, buff, tan, black, yellow, orange, red, green, blue, and white. Each color match is handled on an individual basis. In cases where exact color matching is required, samples of your field raw materials may be required for sample preparation.
Concentration Rates
Prism Pigments Concrete Colors are available specially packaged for your on-site use. Because of the inherent tinting strength of synthetic iron oxides, standard loadings do not exceed 8%. Levels greater than 8% will not enhance the finished color.
Mixing Precautions
Always follow approved mixing practices, which include the following tips:
a) Cement for the entire job/project should be from the same manufacturer. Changes in cement will affect the final color.
b) All aggregate, fine or coarse, should be supplied from one source and non-reactive.
c) The mix design must be consistent from batch to batch. If the batch size is changed the pigment must be also.
d) Concrete slump should not exceed 5″.
e) Clean the drum before and after mixing.
f) Add color directly into the mixer with the other ingredients. Mix 5-10 minutes.
Placement of Concrete Slab Work
As successful slab starts with a will drained subgrade that can sustain the load imposed on the slab. The subgrade should be graded, compacted, dampened. Prevent soft spots, standing water. Minimize handling, movement and spreading of colored concrete for the color consistency. Do not overtrowel, as this will cause darkening. Do not finish until bleed water has left the surface to protect against scaling, efflorescence and uneven coloring.
Placement of Vertical Concrete
Planning is crucial in placement of vertical and poured-in-place concrete. Consider types of cement, detailing of formwork, mixing and placing techniques, slump control and temperature of cure. It is recommended that a field mock-up panel be prepared. Include all materials, reinforcing steel as in the finished project.
Design Criteria for Colored Concrete
The following points should be considered in designing colored concrete. The concrete temperature should be between 65 and 85 degrees. Timing of the arrival of concrete trucks is crucial so that there is no excessive mixing. Avoid using porous forming materials. Conveying methods must be consistent with ACT-304-73. The concrete should be deposited in level lifts 12-18″ thick. The distance between insertions should be generally about 18″ depending on the concrete mix and vibrator used. Tilt-up concrete panels should be textured using sandblasting and surface retarders to expose the course aggregate.
Patching Colored Concrete
Do repair work within two days to minimize color variances. The same materials and methods should be used. It is recommended that a 50/50 mix of white cement/gray cement be used to compensate for the darker patch area. The same color loading should be used on all repairs.
Warranties
Seller warrants that its products will conform to and perform in accordance with the products specifications. This foregoing warranty is in lieu of all other warranties, expressed or implied, including, but not limited to, those concerning merchantability and fitness for a particular purpose. Because of the difficulty in ascertaining and measuring damages hereunder, it is agreed that, except for claims for bodily injury, seller’s liability to the buyer or any third party, arising out of the purchase of the product from seller by buyer shall not exceed the total amount billed and billable to the buyer for the product.
Masonry Color Card
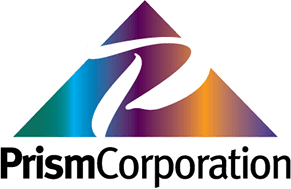
Color Made to Order...For You!
Prism Corporation © | All Rights Reserved | Privacy Policy | Customer Service